How to use hydraulic blockage differential pressure transmitter without error
pageview:3
2025.04.09
The correct usage method of hydraulic blockage differential pressure transmitter
The hydraulic blockage differential pressure transmitter is a key equipment for monitoring the blockage status of filter elements in hydraulic systems. Its correct use requires three aspects: installation, commissioning, and daily maintenance. Firstly, during installation, a suitable position between the inlet and outlet of the oil filter should be selected to ensure that the sensor can accurately sense changes in pressure difference, while staying away from heat sources, vibration sources, and electromagnetic interference sources. During installation, it is necessary to ensure that the pipeline connection is tight to avoid oil or gas leakage that may affect measurement accuracy. Secondly, during the debugging phase, a reasonable pressure difference alarm value (such as 0.35MPa) should be set according to the system operating conditions, and the response sensitivity of the transmitter should be verified through simulated filter blockage testing. When wiring, it is necessary to ensure the stability of the power supply voltage to avoid signal abnormalities caused by voltage fluctuations. At the same time, regular checks should be made to ensure that the circuit connections are secure to prevent signal attenuation caused by poor contact.
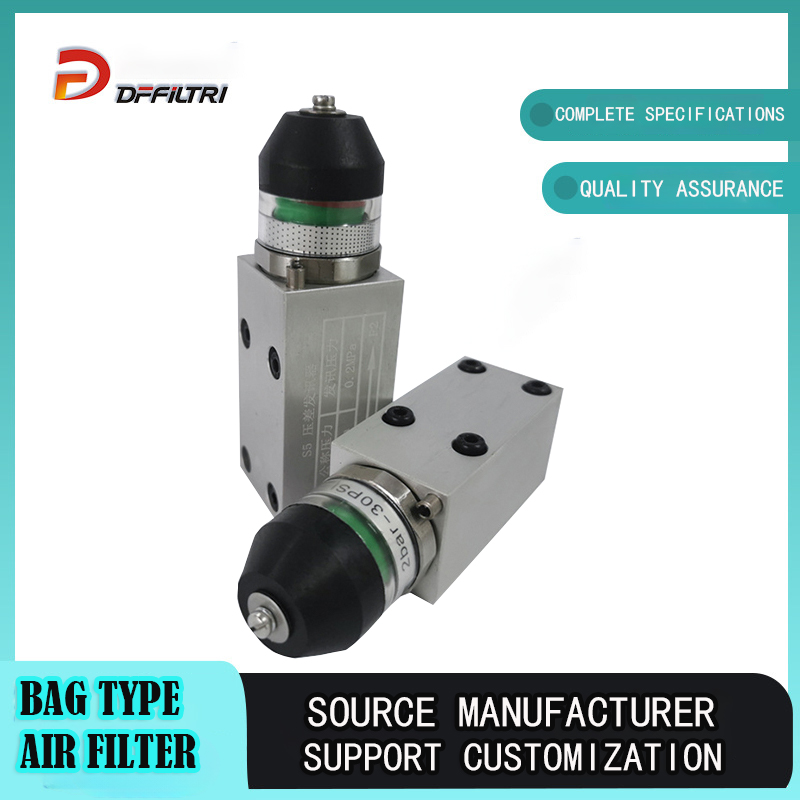
Daily maintenance and fault prevention
To ensure the long-term stable operation of the differential pressure transmitter, it is necessary to establish a regular inspection mechanism. Check the status of the transmitter indicator light daily. When the red button pops up or the signal alarms, the filter element should be cleaned or replaced in a timely manner. Clean the sensors monthly, use specialized cleaning agents to avoid damaging internal components, and check the activity of mechanical components such as springs and pistons to prevent false alarms caused by jamming. When the ambient temperature is too high or too low, temperature control measures should be taken to avoid extreme temperature affecting sensor sensitivity. If there is an abnormal signal output, priority should be given to checking the stability of the power supply and the connection of the circuit. If necessary, replace the damaged signal line. In addition, selecting transmitter models with strong anti pollution capabilities and easy maintenance can significantly reduce failure rates and extend equipment lifespan. Through standardized operations and preventive maintenance, the safe and efficient operation of hydraulic systems can be ensured.kage testing. When wiring, it is necessary to ensure the stability of the power supply voltage to avoid signal abnormalities caused by voltage fluctuations. At the same time, regular checks should be made to ensure that the circuit connections are secure to prevent signal attenuation caused by poor contact.